

What we do
Friese heat treats parts that are produced in its factory and provides this service to third parties. All The stages of our process are carried out in accordance with the most rigorous quality standards and rules, performed by highly trained professionals, which guarantees a superior quality product.
Every detail is important, and every phase of our process is designed to satisfy the individual needs of our customers.
The continuous technological innovations in the process are the result of research and improvements, made possible by our four decades of operation.
Friese heat treats parts that are produced in its factory and provides this service to third parties. All The stages of our process are carried out in accordance with the most rigorous quality standards and rules, performed by highly trained professionals, which guarantees a superior quality product.
Every detail is important, and every phase of our process is designed to satisfy the individual needs of our customers.
The continuous technological innovations in the process are the result of research and improvements, made possible by our four decades of operation.
Services
Vacuum hardening is a process used to strengthen and improve the mechanical properties of metal parts. It is widely used to increase the hardness, wear resistance, toughness and durability of various components.
The vacuum hardening process takes place in a specially designed vacuum chamber, where metal parts are subjected to a controlled heat treatment.
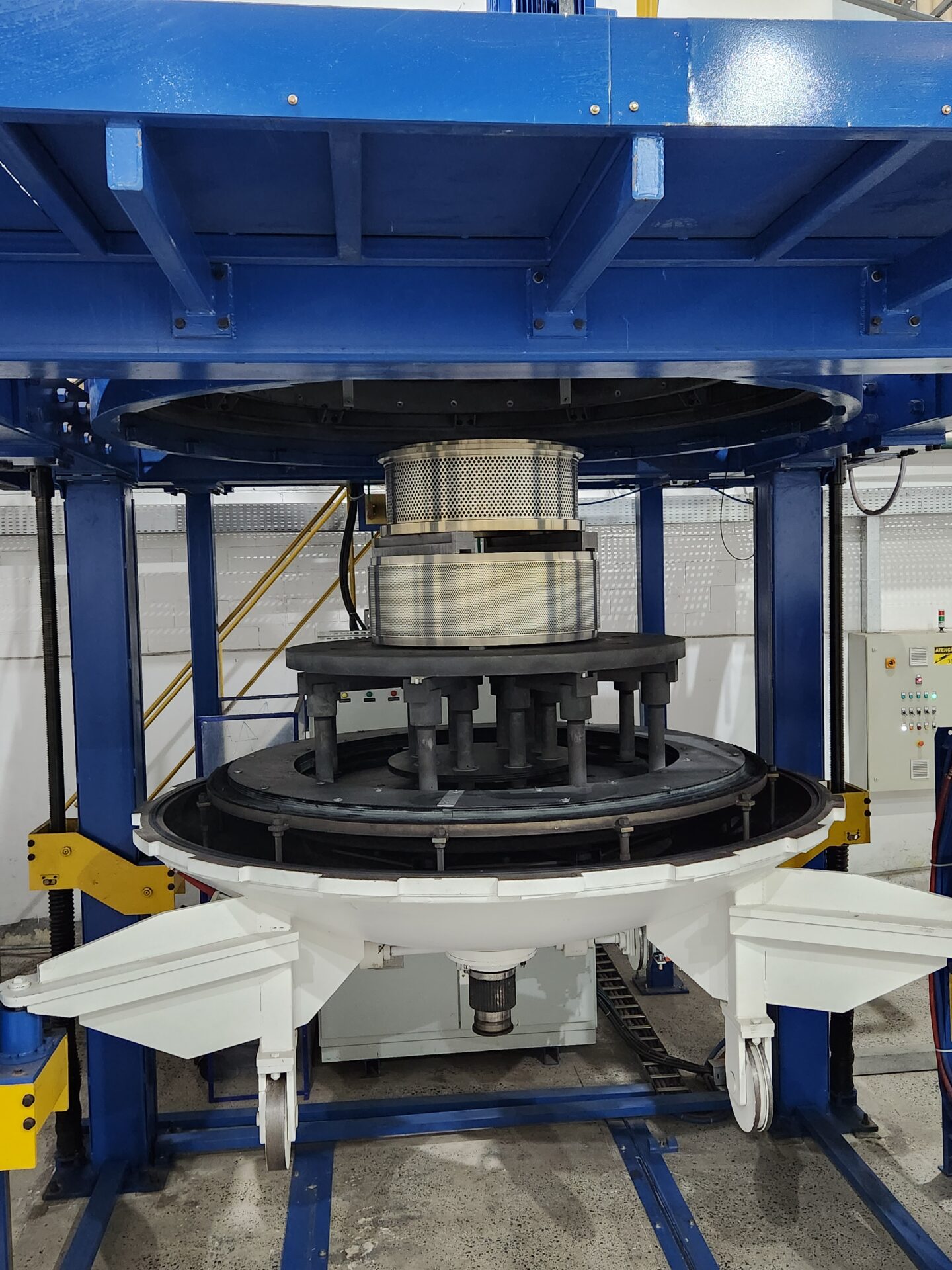
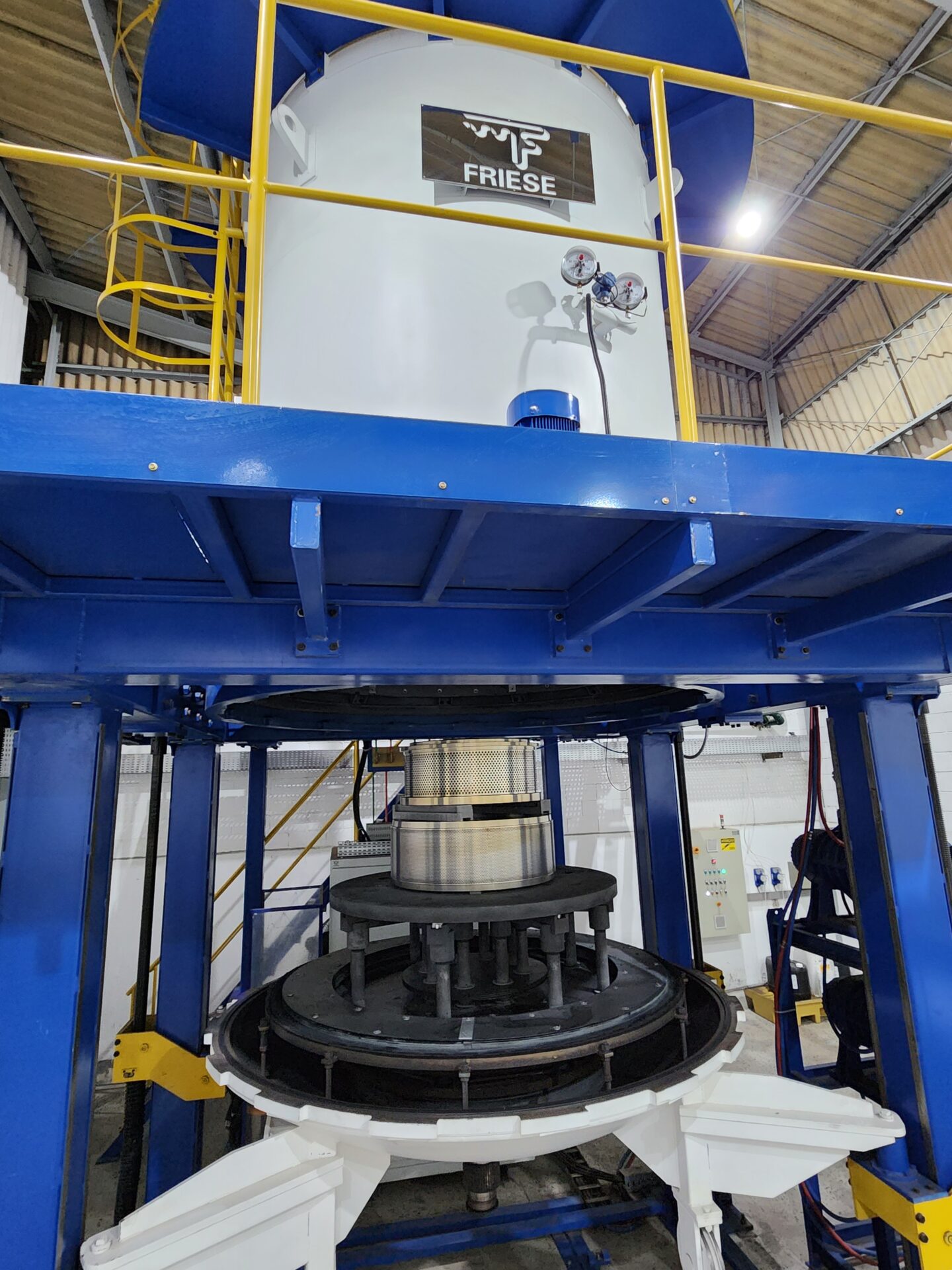
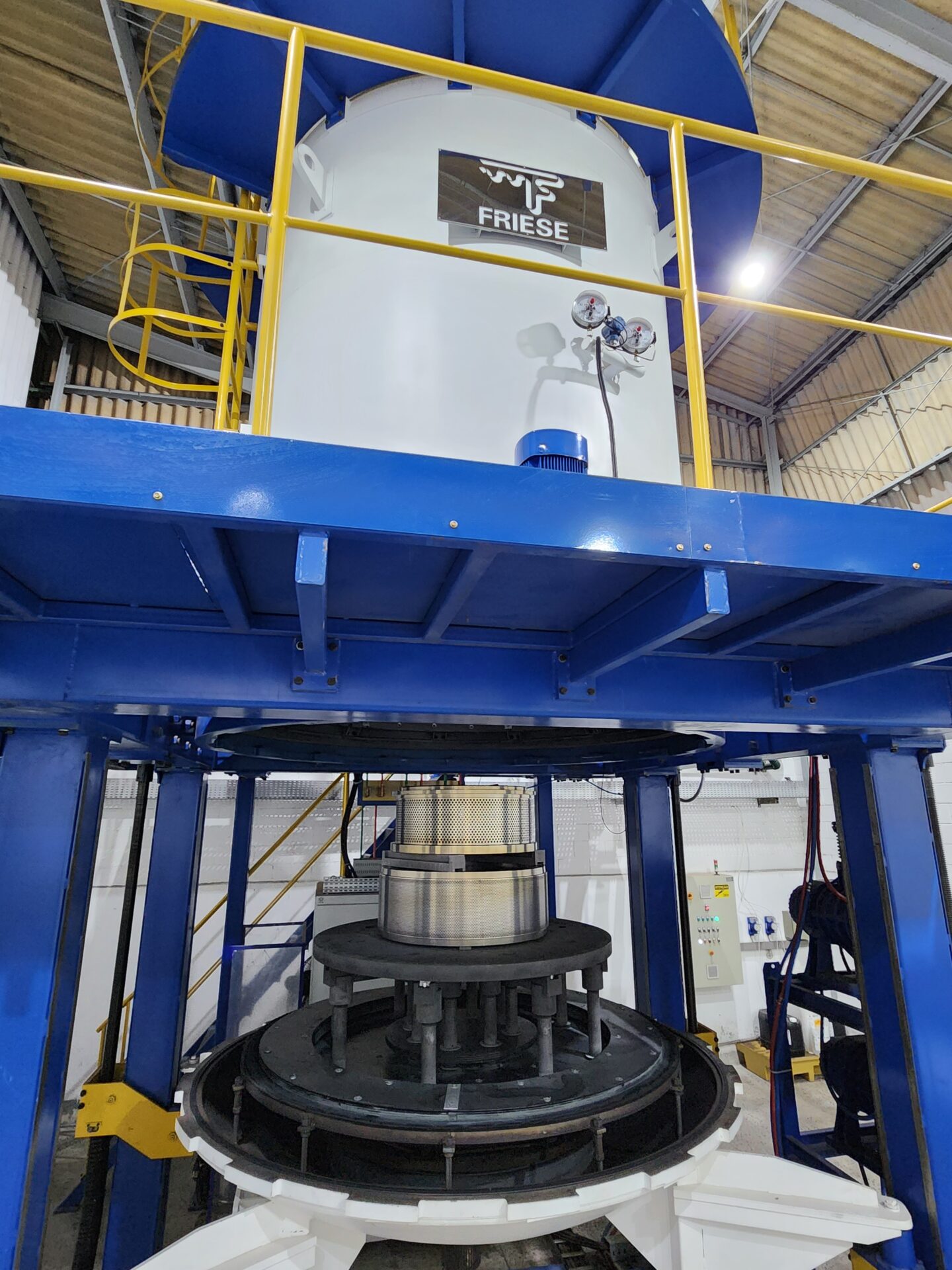
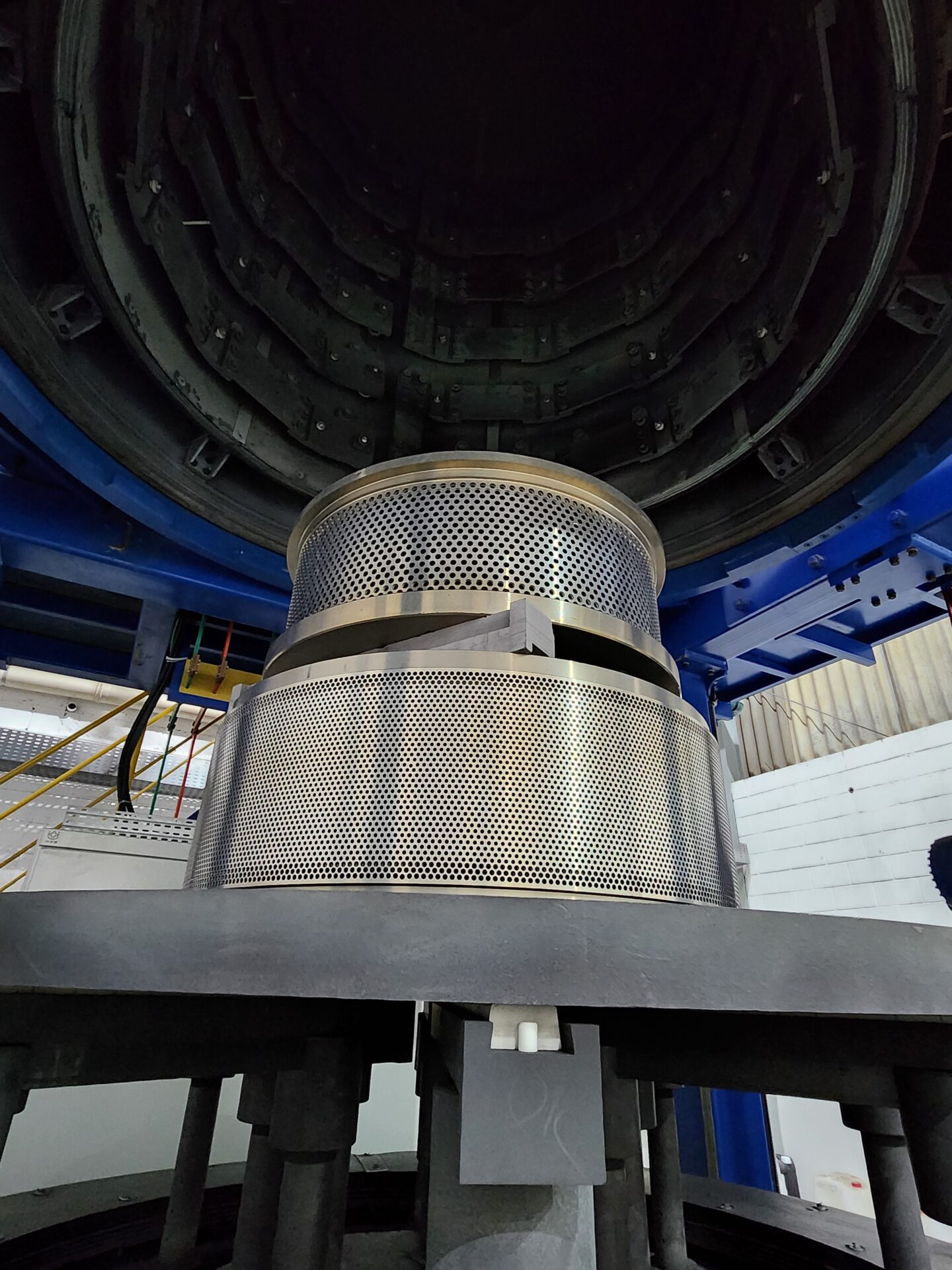
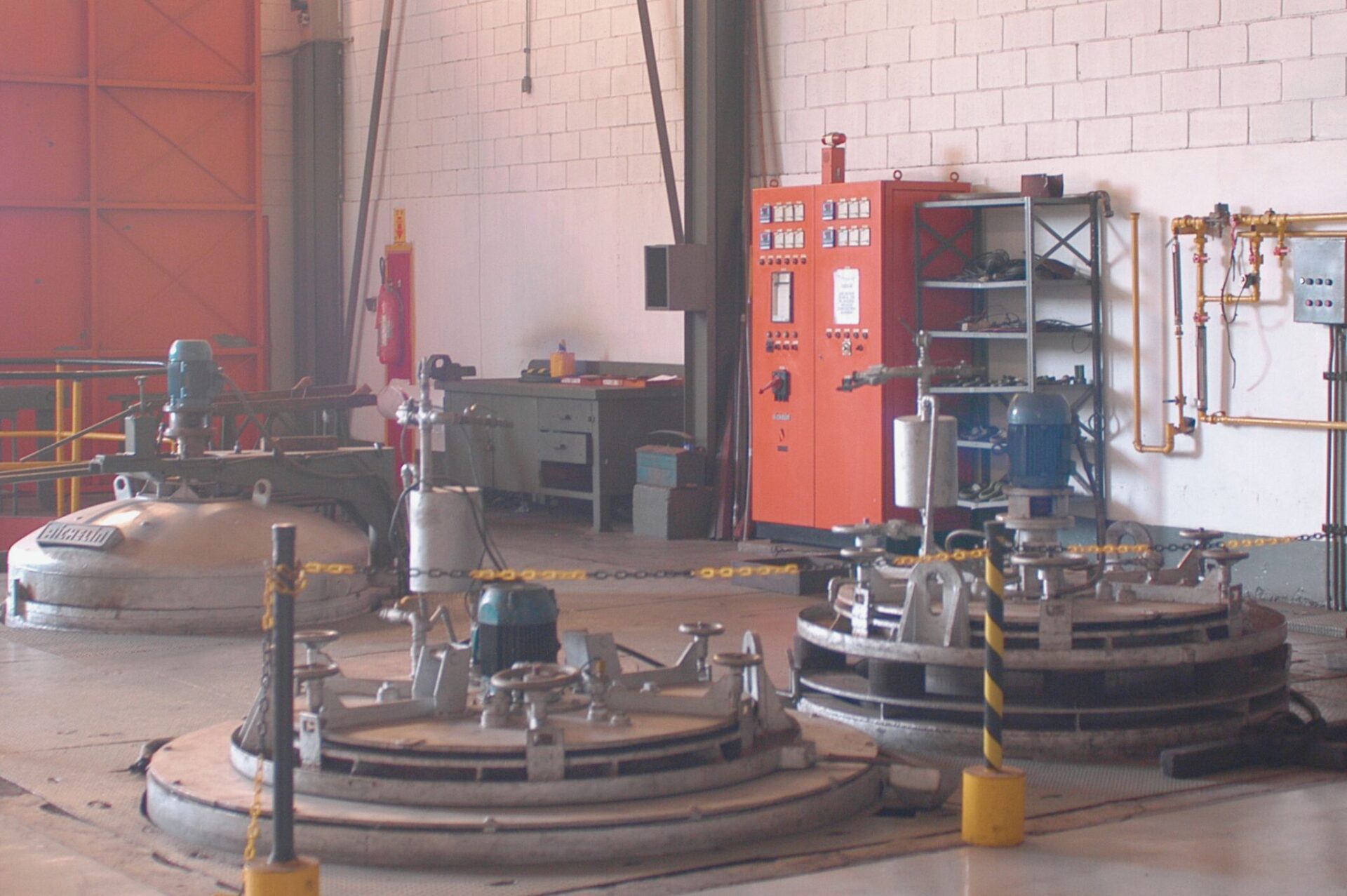
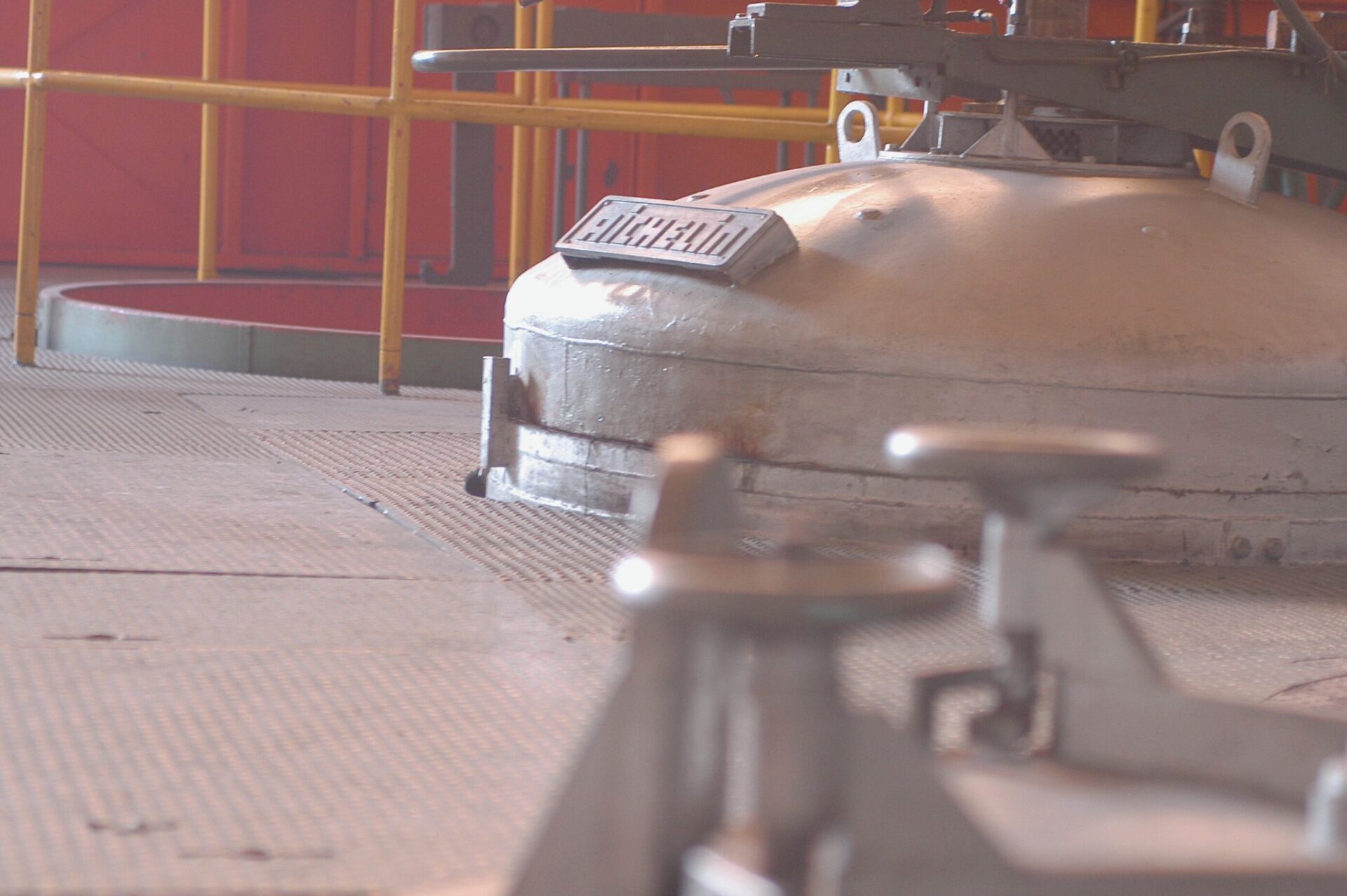
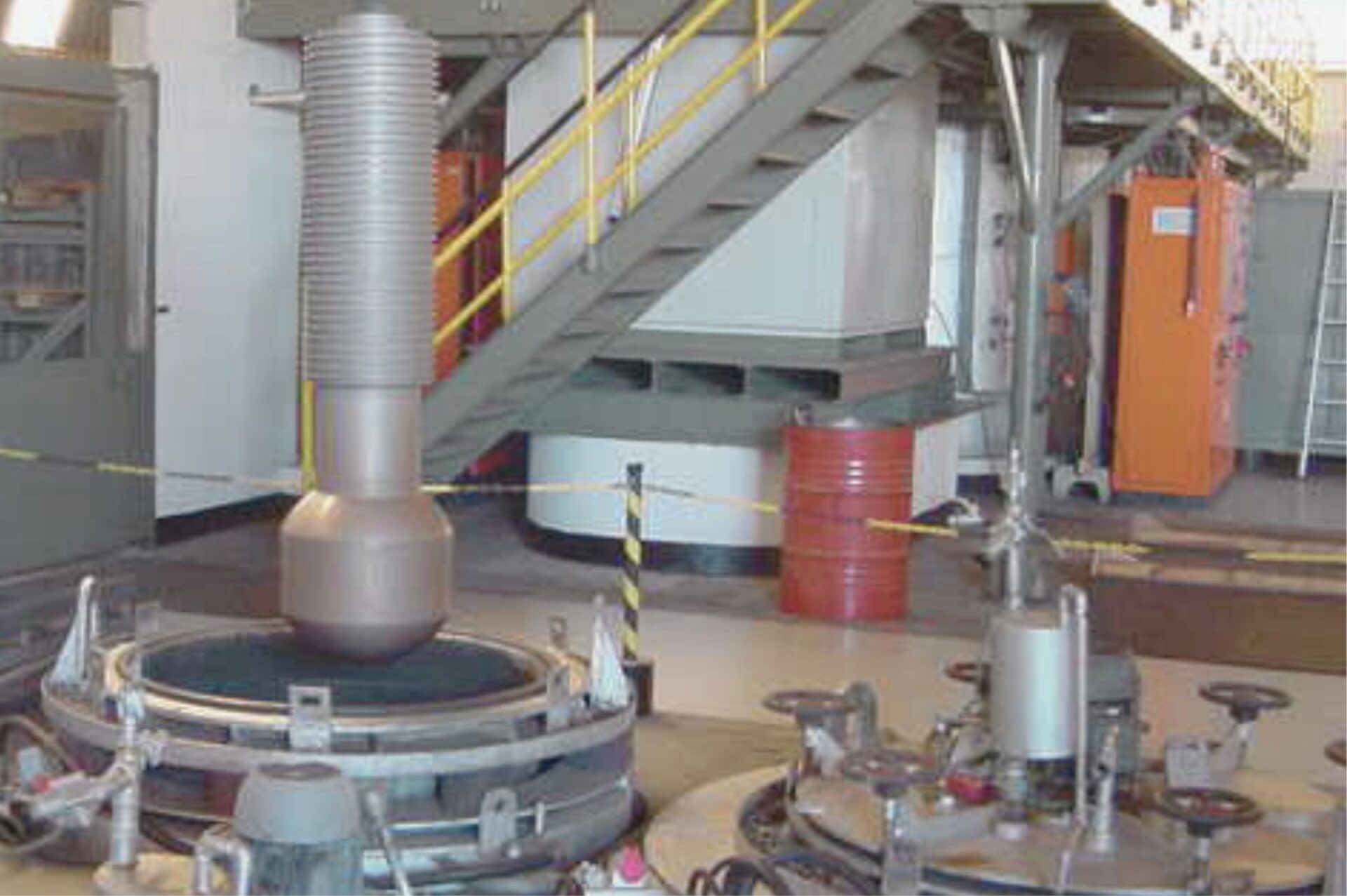
Thermochemical treatment in which surface enrichment with carbon is promoted.
This process is carried out on materials with a low percentage of carbon, consisting of introducing it into the surface of the steel, so that it achieves a high surface hardness and its core also increases in hardness. At Friese, this process is carried out in a gaseous medium.
Thermal treatment characterized by cooling at a speed higher than the critical quenching speed of a ferrocarbon alloy, starting from a temperature above the critical zone for hypoeutectoid steels and, generally, within the critical zone, for hopereutetoid steels, resulting in the transformation of austenite into martensite
At Friese, cooling is carried out in the Martempera, aiming to reduce distortions arising from the cooling process.
Thermal treatment of a tempered part is characterized by reheating below the critical zone and adequate cooling. It aims to adjust the requested hardness, eliminate brittleness, increase ductility and shock resistance.
Induction is the tempering heat treatment, whose heating operation is carried out quickly and localized, followed by rapid cooling. This process provides surface and/or localized hardening of the part.
U Main characteristics of surface tempering:
- Superficial and/or localized hardening;
- Possibility of selecting the region to be hardened;
- Core characteristics are not affected;
- Increased wear resistance;
- Increased resistance to fatigue;
- Reduction of deformations due to the smaller treated region;
- Reduction of manufacturing costs;
- Allows localized hardening of case-hardened steels.
Among the applications of this process, we perform:
- Lamination cylinders;
- Gear teeth;
- Suspension pins for the automotive industry;
- Screw heads;
- Steel tubes for the mining industries;
- Lathe bus;
- Industrial knives;
- Machine guide ruler;
- Gearshift forks.
Thermochemical treatment in which surface enrichment with nitrogen is promoted. The hardness, layer and deformation results obtained after this process are influenced by several factors, including:
- Type of steel: alloying elements increase the hardness of Nitriding, therefore, each type of steel presents a different layer and hardness result;
- Heat treatments prior to Nitriding: If the product has been processed or tempered at a temperature close to 620ºC, its results will be better and its deformation will be lower.
- Pre-machining: A part that has had a large amount of material removed without having undergone stress relief tends to present greater deformation during Nitriding.
- Protection: The regions (of the parts) that should not be Nitrided are painted with a specific paint to prevent the penetration of Nitrides, these areas must be A symbol of innovation, quality and excellence in its sector.
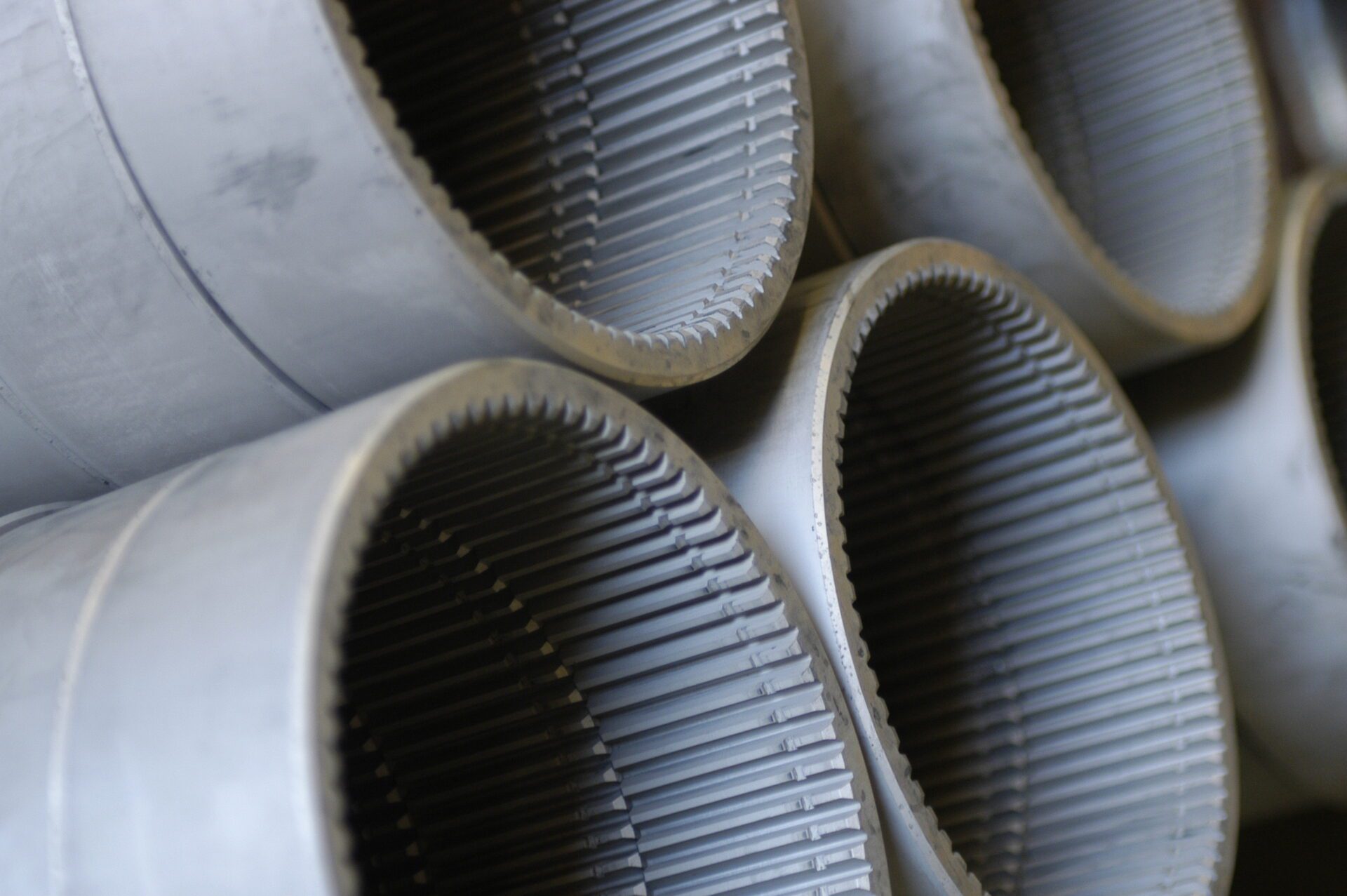
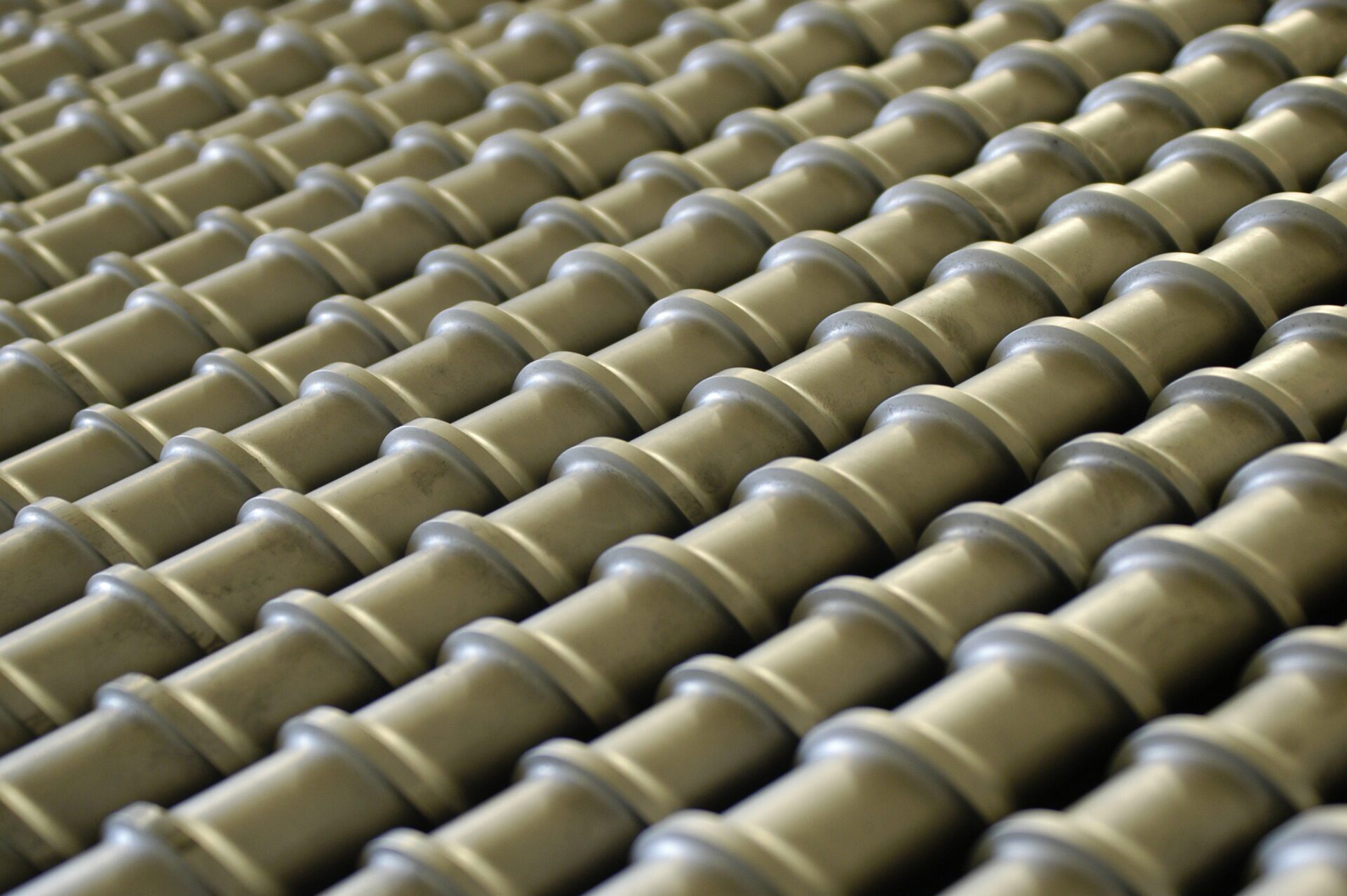
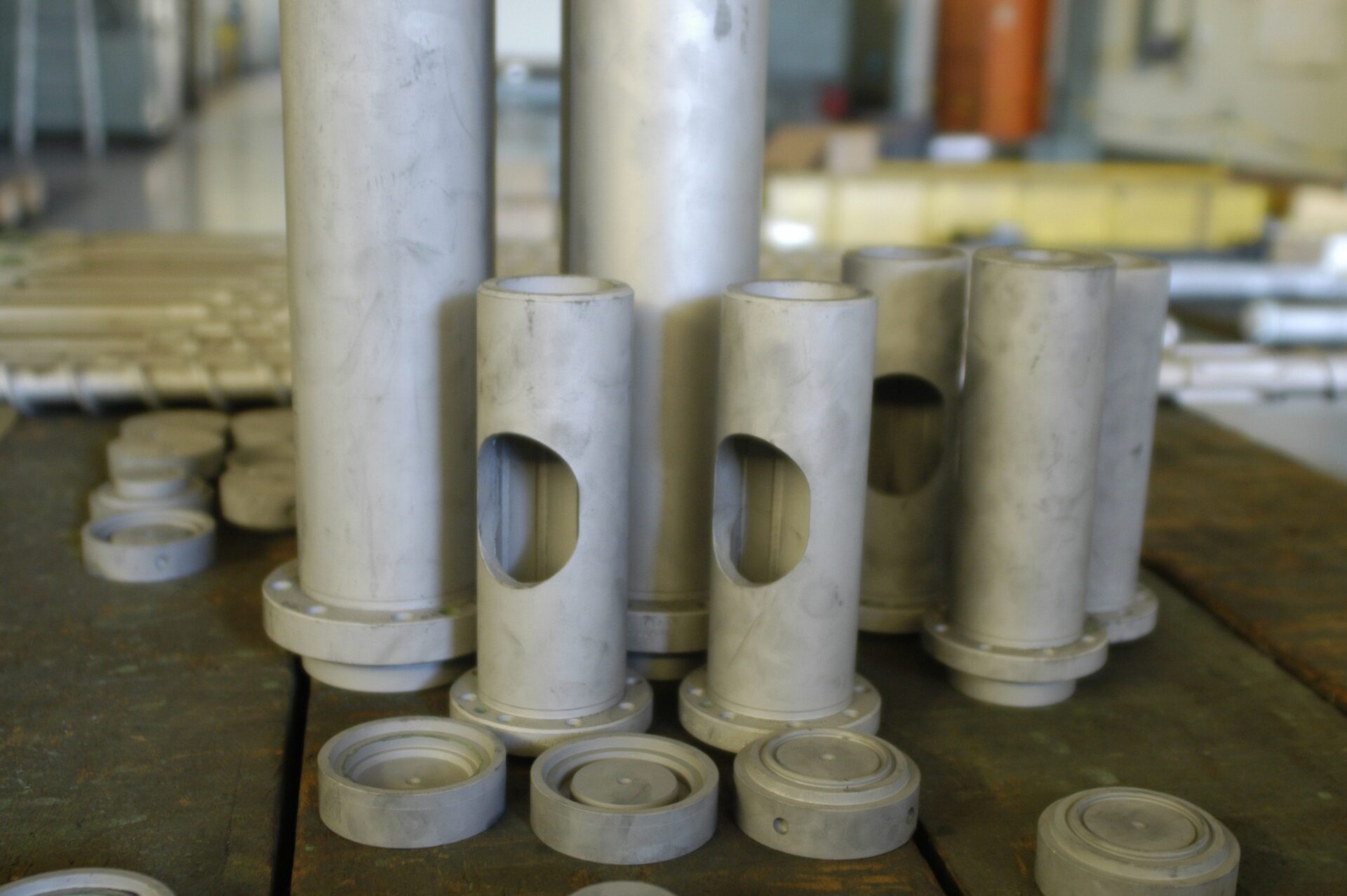
Vacuum hardening is a process used to strengthen and improve the mechanical properties of metal parts. It is widely used to increase the hardness, wear resistance, toughness and durability of various components.
The vacuum hardening process takes place in a specially designed vacuum chamber, where metal parts are subjected to a controlled heat treatment.
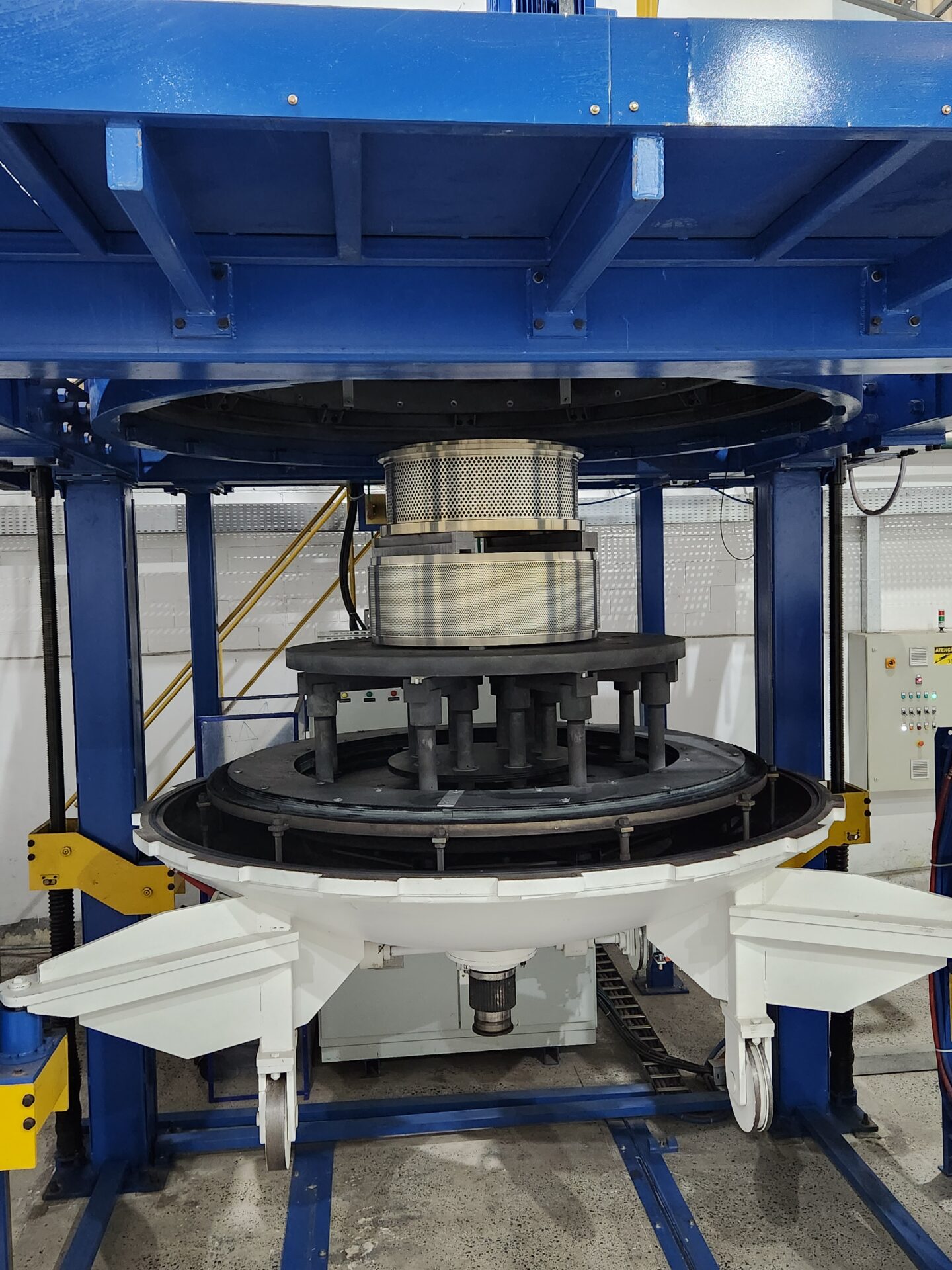
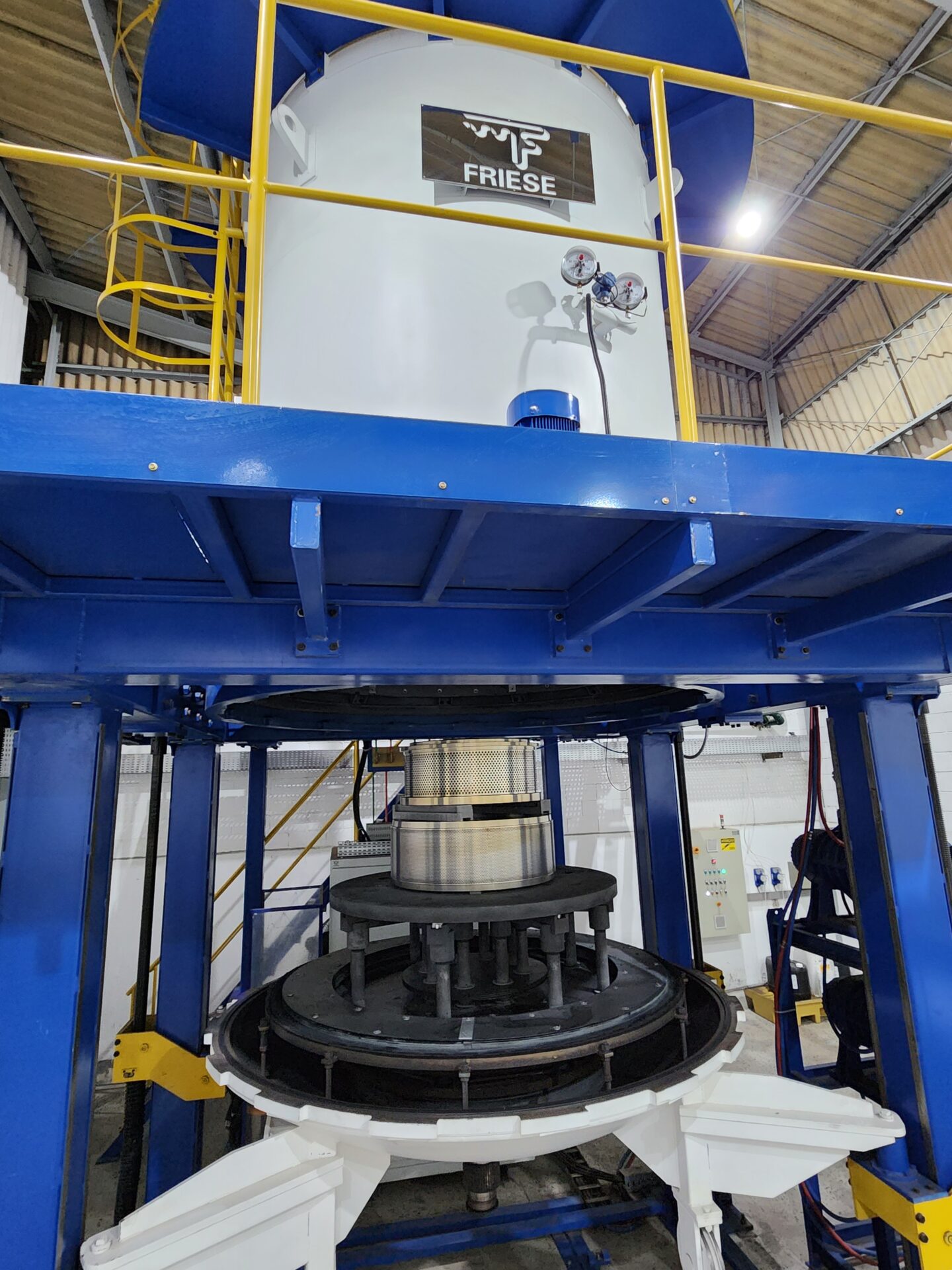
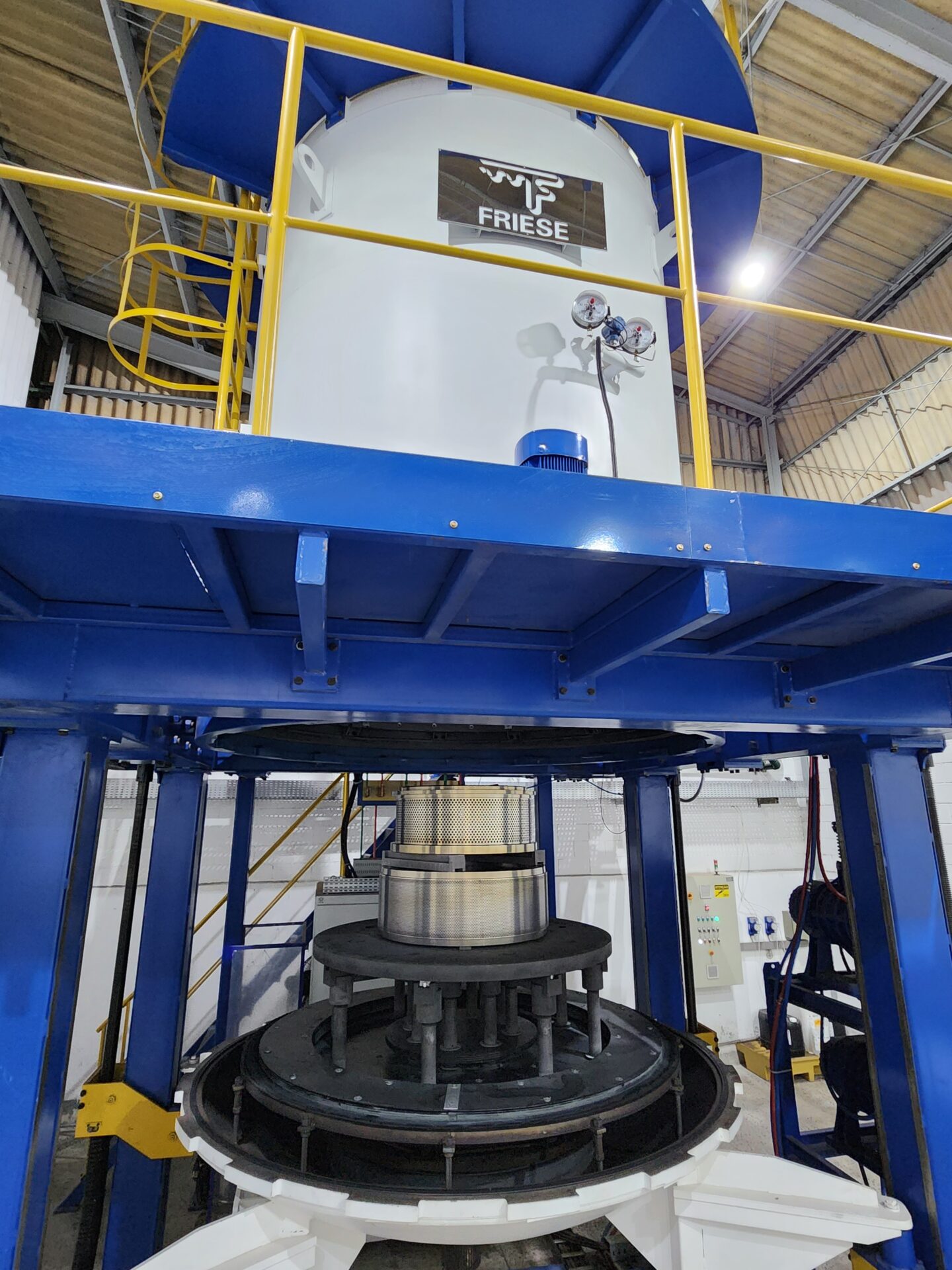
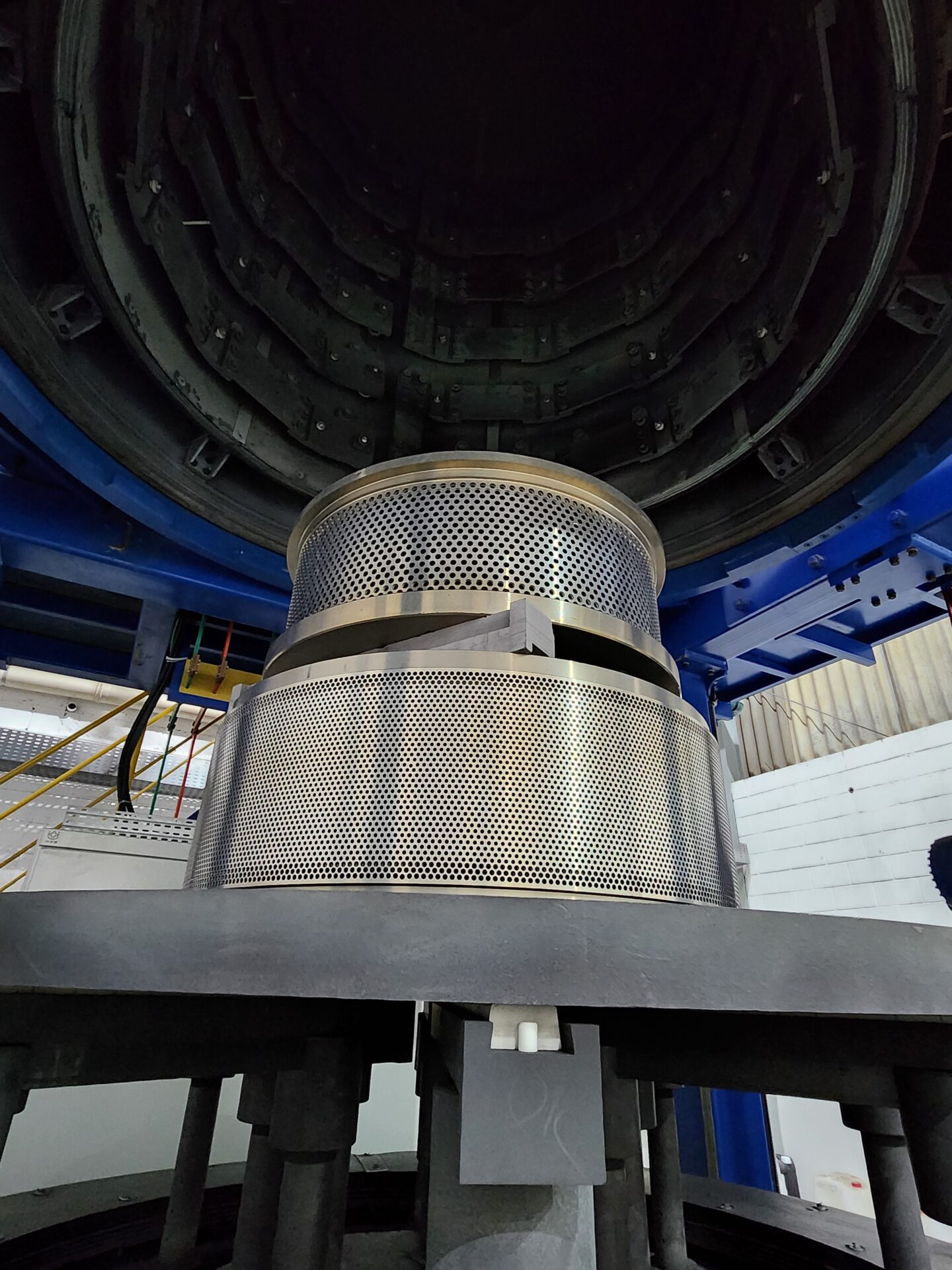
The aim is to relieve stresses produced by cold mechanical transformations, such as stamping, straightening, flame cutting, welding or machining.
The temperatures used are lower than those in the critical zone. Its threshold temperature must be related to the type of treatment previously carried out on the part, so that it does not modify its structure and does not cause changes to its mechanical properties.
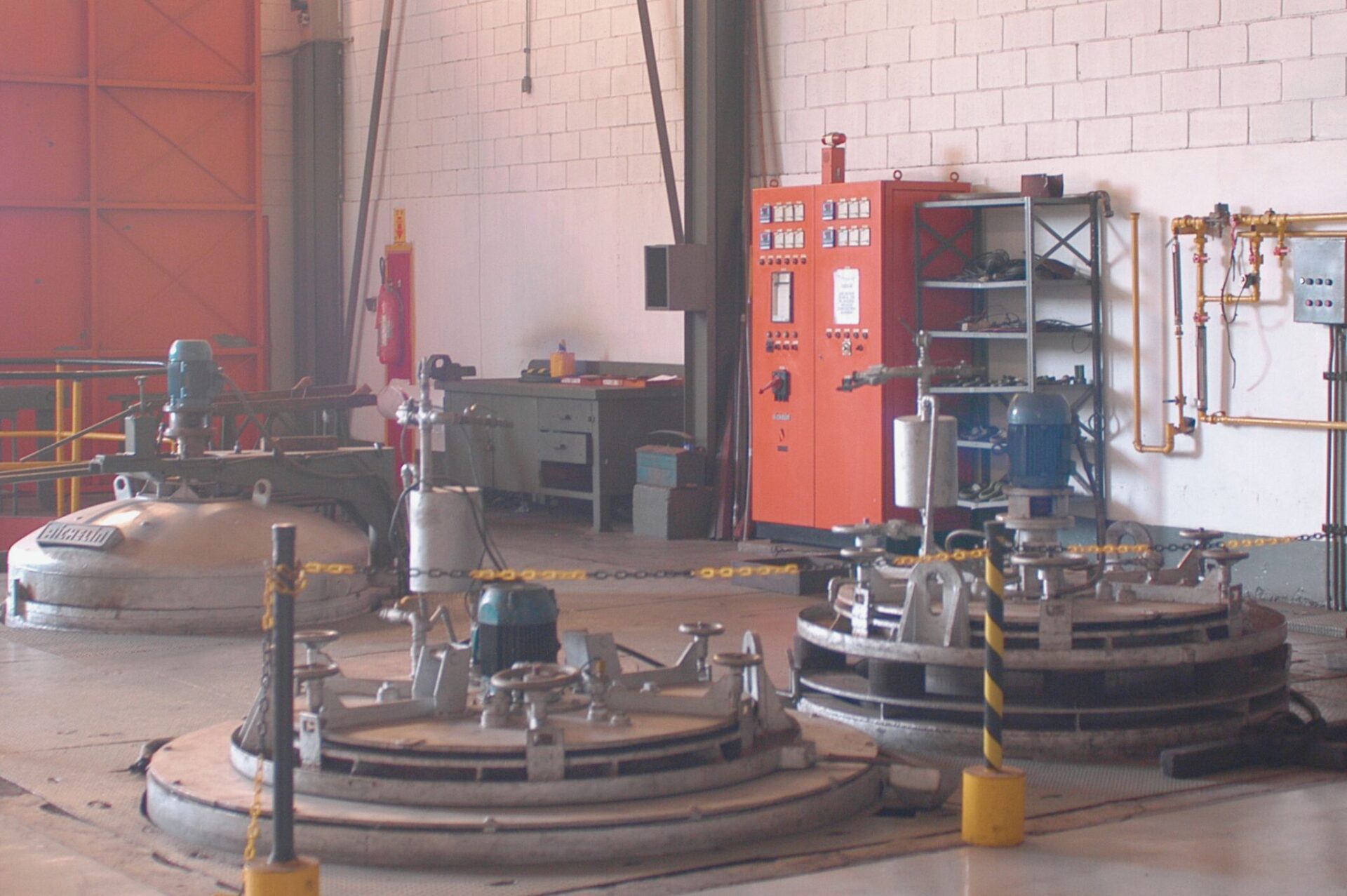
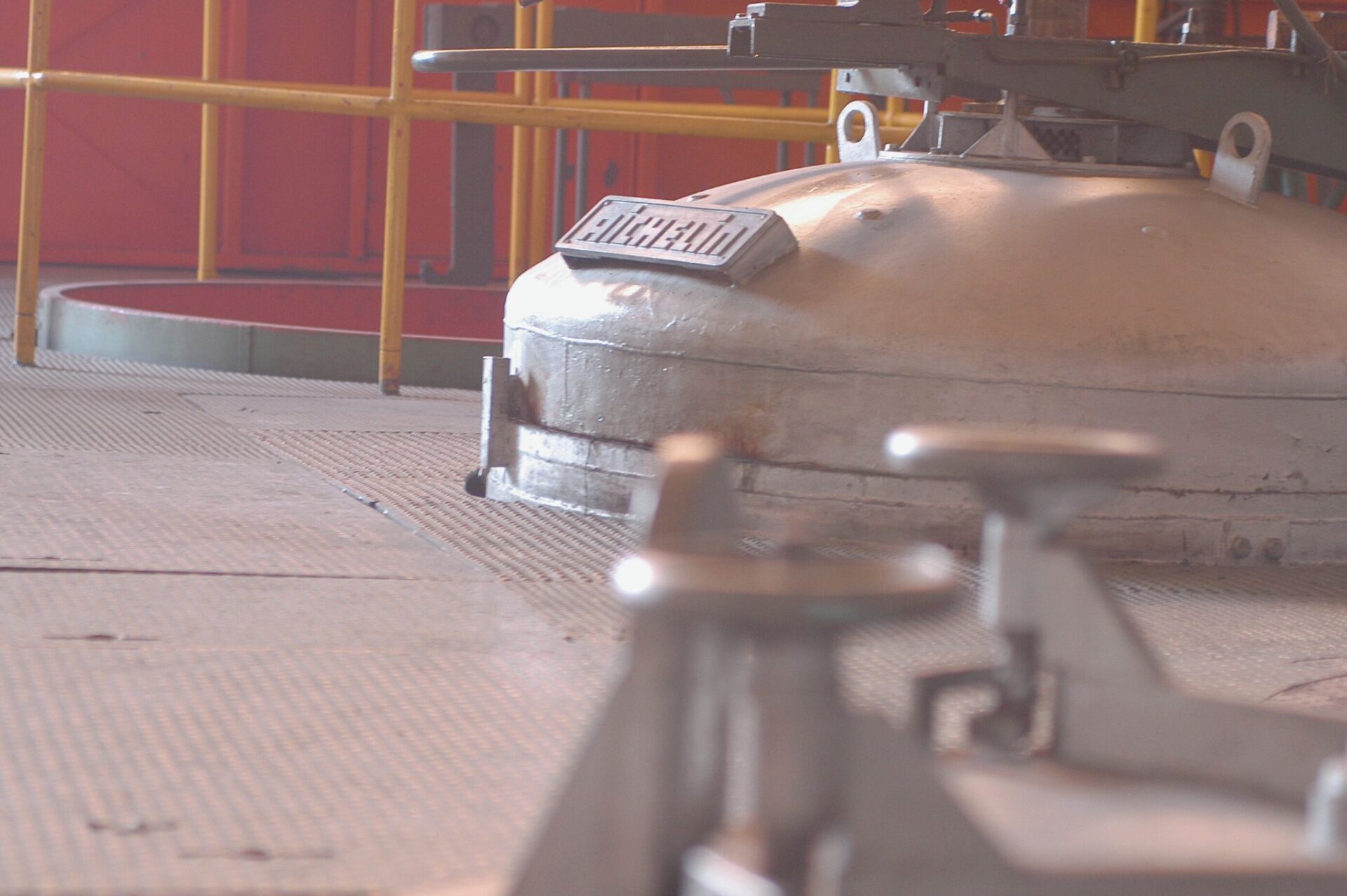
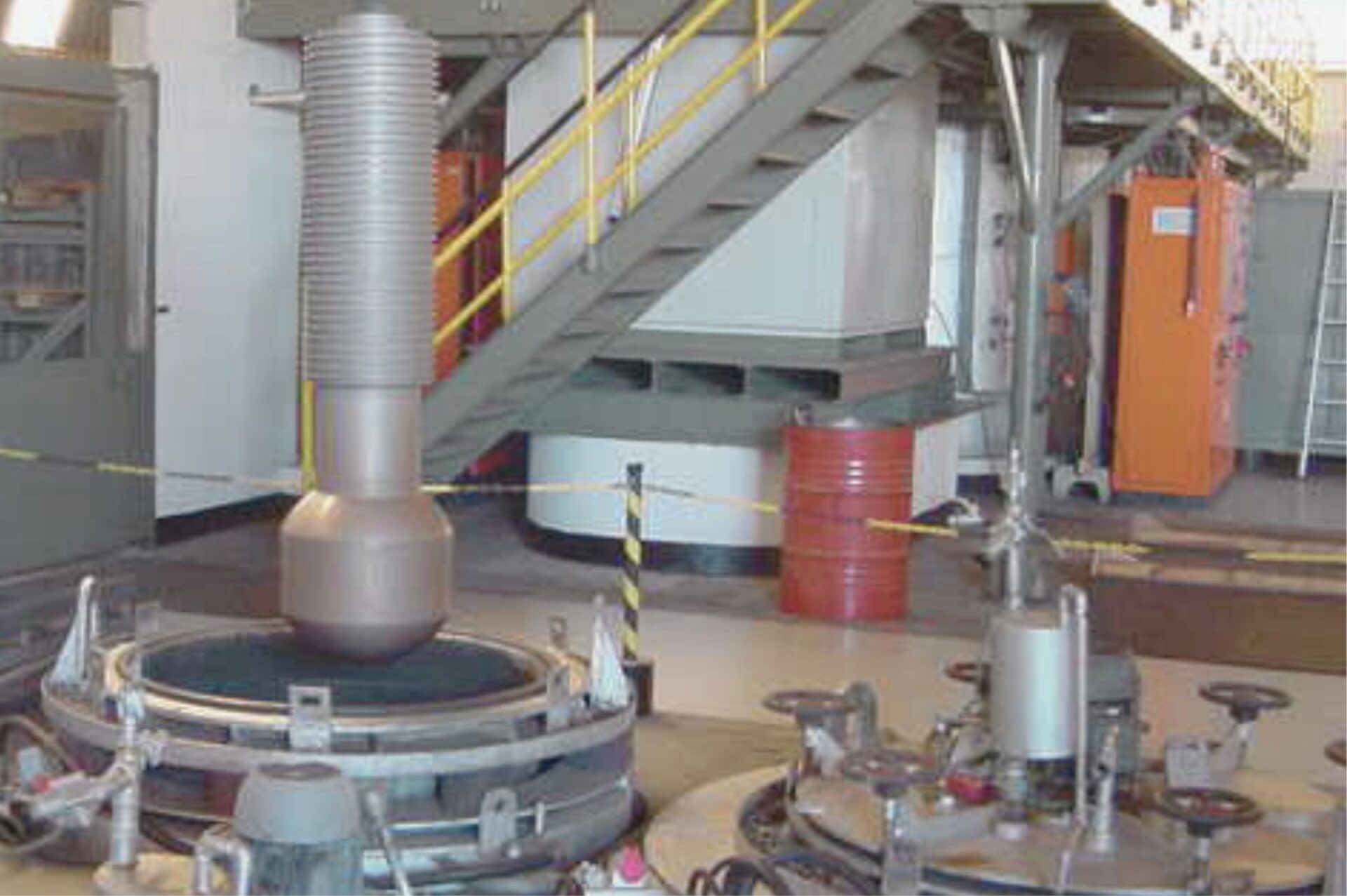
Thermochemical treatment in which surface enrichment with carbon is promoted.
This process is carried out on materials with a low percentage of carbon, consisting of introducing it into the surface of the steel, so that it achieves a high surface hardness and its core also increases in hardness. At Friese, this process is carried out in a gaseous medium.
Thermal treatment characterized by cooling at a speed higher than the critical quenching speed of a ferrocarbon alloy, starting from a temperature above the critical zone for hypoeutectoid steels and, generally, within the critical zone, for hopereutetoid steels, resulting in the transformation of austenite into martensite
At Friese, cooling is carried out in the Martempera, aiming to reduce distortions arising from the cooling process.
Thermal treatment of a tempered part is characterized by reheating below the critical zone and adequate cooling. It aims to adjust the requested hardness, eliminate brittleness, increase ductility and shock resistance.
Thermal treatment of a tempered part is characterized by reheating below the critical zone and adequate cooling. It aims to adjust the requested hardness, eliminate brittleness, increase ductility and shock resistance.
Induction is the tempering heat treatment, whose heating operation is carried out quickly and localized, followed by rapid cooling. This process provides surface and/or localized hardening of the part.
U Main characteristics of surface tempering:
- Superficial and/or localized hardening;
- Possibility of selecting the region to be hardened;
- Core characteristics are not affected;
- Increased wear resistance;
- Increased resistance to fatigue;
- Reduction of deformations due to the smaller treated region;
- Reduction of manufacturing costs;
- Allows localized hardening of case-hardened steels.
Among the applications of this process, we perform:
- Lamination cylinders;
- Gear teeth;
- Suspension pins for the automotive industry;
- Screw heads;
- Steel tubes for the mining industries;
- Lathe bus;
- Industrial knives;
- Machine guide ruler;
- Gearshift forks.
Thermochemical treatment in which surface enrichment with nitrogen is promoted. The hardness, layer and deformation results obtained after this process are influenced by several factors, including:
- Type of steel: alloying elements increase the hardness of Nitriding, therefore, each type of steel presents a different layer and hardness result;
- Heat treatments prior to Nitriding: If the product has been processed or tempered at a temperature close to 620ºC, its results will be better and its deformation will be lower.
- Pre-machining: A part that has had a large amount of material removed without having undergone stress relief tends to present greater deformation during Nitriding.
- Protection: The regions (of the parts) that should not be Nitrided are painted with a specific paint to prevent the penetration of Nitrides, these areas must be A symbol of innovation, quality and excellence in its sector.
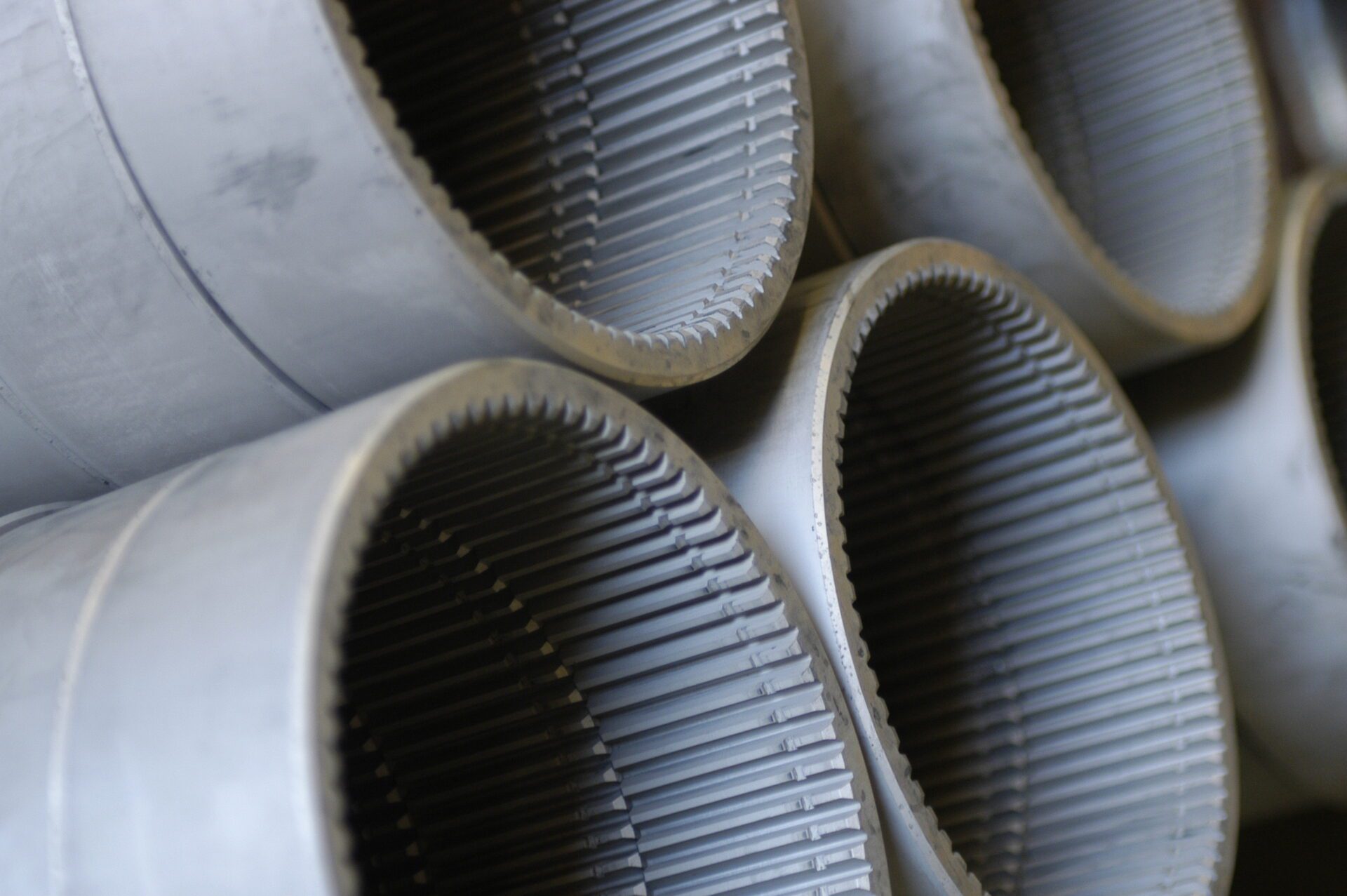
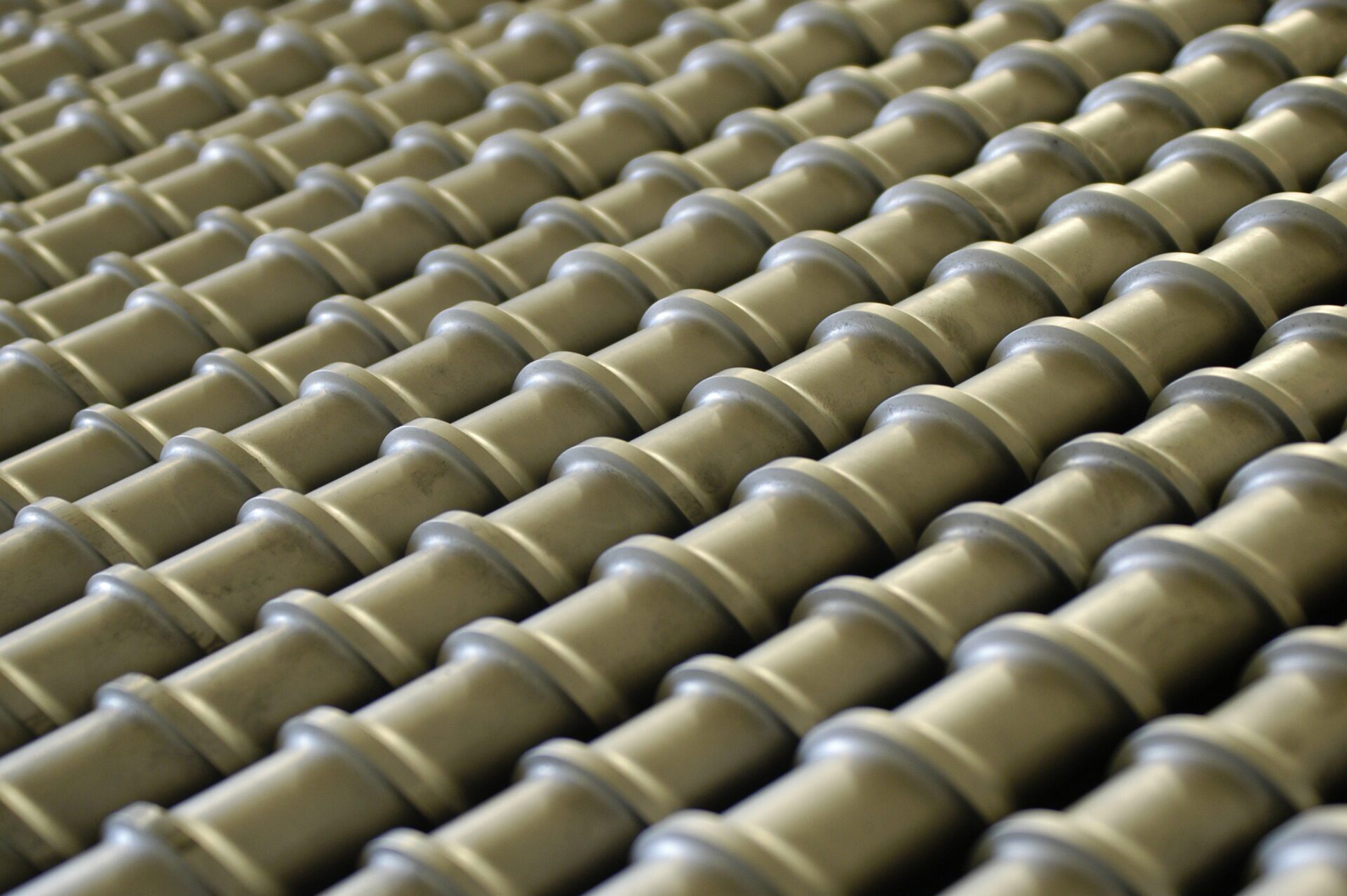
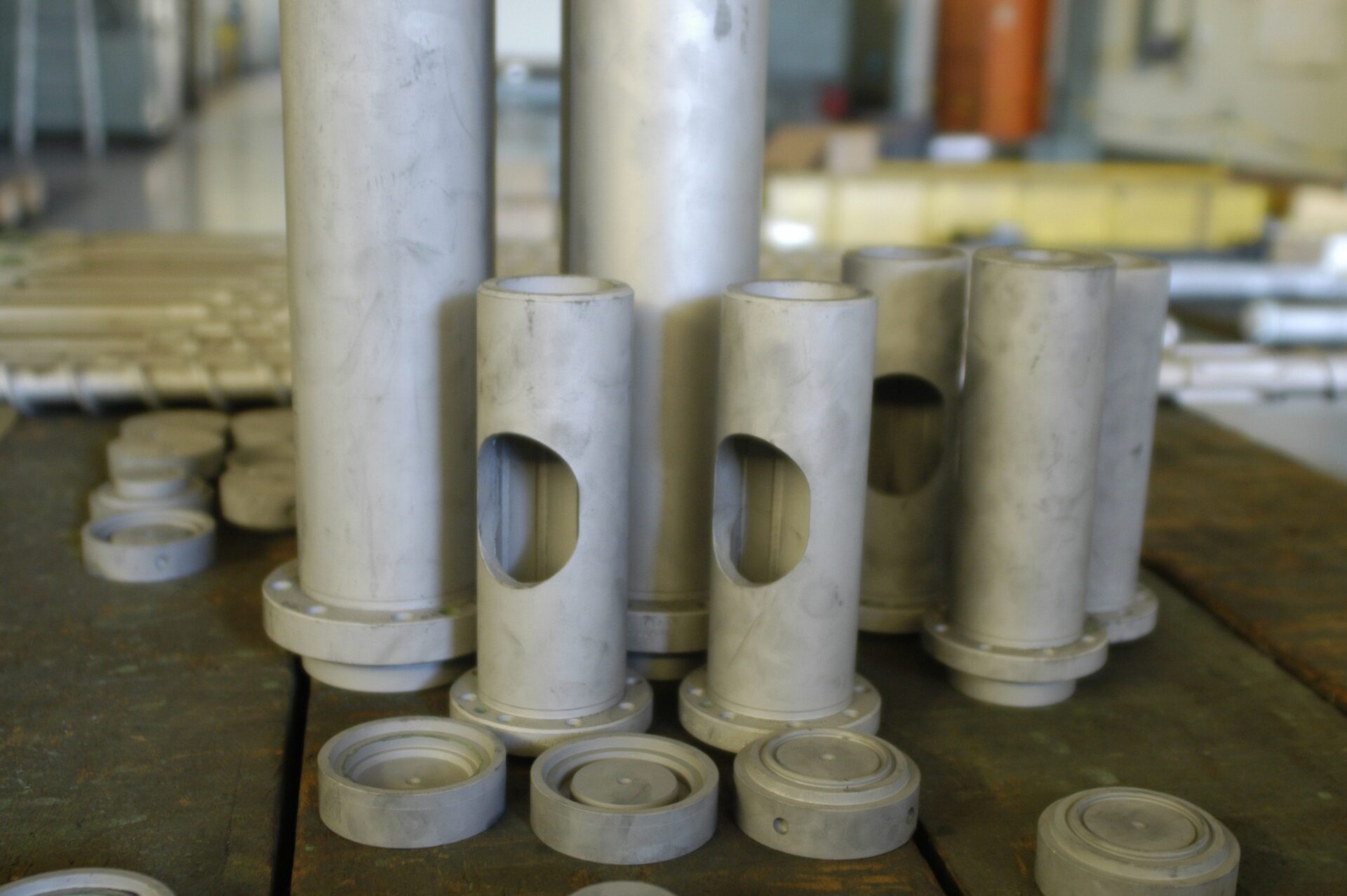